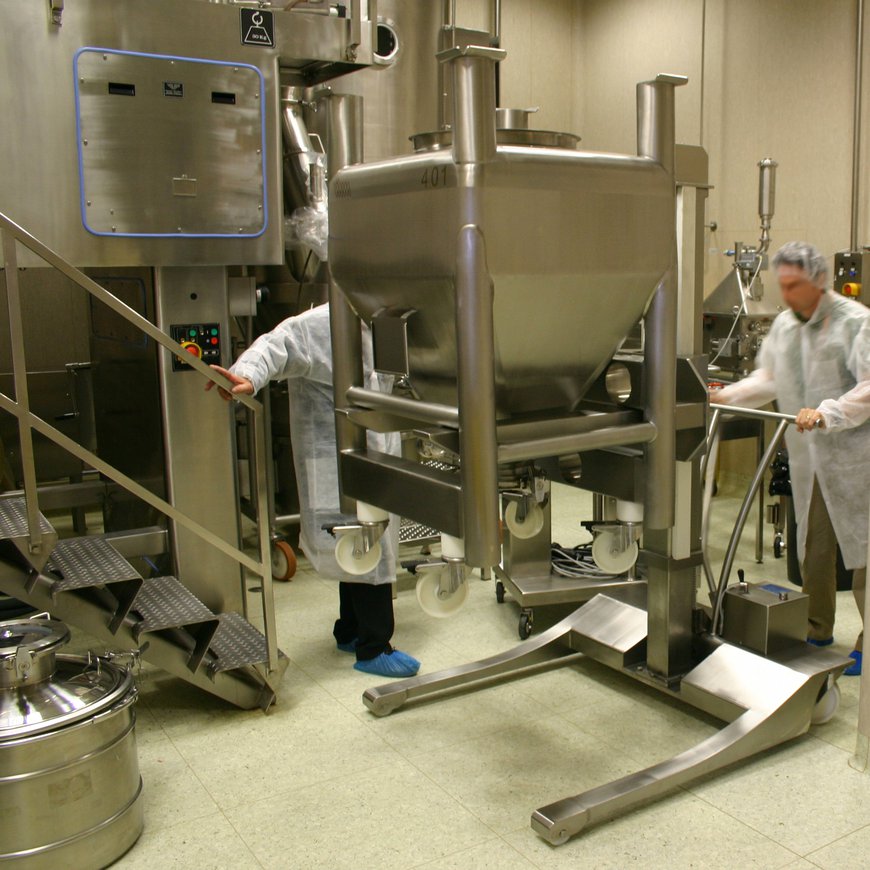
One of the primary objectives of pharmaceutical companies is the prevention of microbial and chemical contamination. However, solving the problem is no small matter.
The contamination – differing in type and quantity - refers to the presence of undesirable substances inside the products and in work environments. It can be generated by multiple factors including the choice of raw materials, the equipment used, the processing place, clothing and personnel operations.
This is why pharmaceutical companies are equipped with Cleanrooms, that is a controlled environment that has a low level of pollutants such as dust, airborne microbes, aerosol particles, and chemical vapors. To be exact, a cleanroom has a controlled level of contamination that is specified by the number of particles per cubic meter at a specified particle size.
Cleanrooms are used in practically every industry where small particles can adversely affect the manufacturing process.
A cleanroom is any given contained space where provisions are made to reduce particulate contamination and control other environmental parameters such as temperature, humidity and pressure.
In the Cleanrooms both the personnel and the equipment used must follow particular precautions.
In this case it is very important that the clothes worn and the dressing procedure of the operators are adequate. First of all the garments must have a low particle release and a high filtration capacity against the contamination generated by man; personnel selected to work in cleanrooms undergo extensive training in contamination control theory. They enter and exit the cleanroom through airlocks, air showers and/or gowning rooms, and they must wear special clothing designed to trap contaminants that are naturally generated by skin and the body. Cleanroom clothing is used to prevent substances from being released off the wearer’s body and contaminating the environment. The cleanroom clothing itself must not release particles or fibers to prevent contamination of the environment by personnel.
The way workers get dressed is strictly related to the level of cleanliness and sterility of the environment in which one must operate. However, it is good practice to sanitize your hands with an appropriate product, remove the dirt from the footwear by walking on the appropriate mat, wear the cap, the shoe covers, the mask, and finally overalls or shirts and gloves if necessary. During all these operations care must be taken not to contaminate clothing by making it touch the floor or walls.
All the instruments and equipment used in the cleanroom (and not only there) must take into account specific hygiene requirements in addition to those of functionality and safety. Companies should therefore operate preferably with equipment that is not only manageable and versatile, but also easy to clean and maintain.
In fact, the care and hygiene of the instruments will be greater and greatly facilitated if planned during the design phase.
In actually means, for instance, to include machines with smooth surfaces, continuous and polished welds, precise assemblies, and therefore very few cracks or dead spaces where processing residues can be trapped. All this in order to avoid the survival and the multiplication of the microorganisms contained in them.
In the design phase all those parts that need lubrication or greasing should be reduced to a minimum and, where necessary, it would be advisable to use only lubricants certified for accidental contact with NSF H1 (National Sanitation Foundation) foods and obtained from raw materials complying with the Food and Drug Administration (FDA).
The choice of equipment construction materials is also important. In addition to having good mechanical characteristics (strength, resilience and hardness), they must be inert and non-toxic and therefore compatible with ingredients and products.
For this purpose it is preferable to use AISI 304/316 stainless steel for the structures, while for sliding surfaces, plastic materials such as polyethylene terephthalate (PET) or acetal resin (POM) will be used. All these materials are in fact resistant to the chemical aggression of oils, fats, preservatives, detergents and disinfectants.
To conclude the prevention of the problem of contamination - closely related to the factors explained above - if on the one hand it appears expensive, on the other hand it guarantees considerable savings in terms of energy and money to the pharmaceutical companies. This is done first of all by avoiding the waste of non-compliant product batches, and secondly by ensuring optimization of processing times due to a substantial drop in production downtime required to make work environments suitable.